Mechanical Properties of High Density Low Alloyed PM Steels: Effect of Sintering and Secondary Heat Treatments
Nowadays sintered components are widely used for different applications. One of the biggest end user is the automotive industry. The growth of the PM Industry in recent years can to a very large extent be explained by the shaping ability of PM processes.
In this work the mechanical properties of two main low alloyed PM steel groups were studied as a function of density, sintering temperature and microstructure (modified by carbon content and either heat or thermochemical treatment). The former group is based on the Fe-Mo-(Ni) system, widely used in the industry today and the latter is based on Astaloy CrL prealloyed powder based on the Fe-Cr system. Astaloy CrL was designed as complement or replacement to powders based on common Fe-Mo-Ni-Cu systems used for medium-to-high strength applications.
The purpose of this study was to check how the mechanical properties (tensile, impact and fatigue resistance) of materials are influenced by the processing conditions investigated, through their effect on density, porosity and microstructure.
Different methods to obtain high density, such as warm compaction and high velocity compaction were used, the results in any case were compared to convectional (cold) compacted materials.
Generally, the sintering during this project was carried out in 90%N2/10%H2 atmosphere at 1120 (belt furnace) and 1250ºC (batch furnace) for 30 min. Some additional high temperature sintering tests were carried out in an industrial vacuum furnace, with different cooling rate.
Experiments with different secondary heat treatments, such as through hardening, steam oxidation and carburizing, subjected to improve the material’s performance were carried out.
CONSULTA INTEGRALMENTE QUESTA TESI
La consultazione è esclusivamente in formato digitale .PDF
Acquista
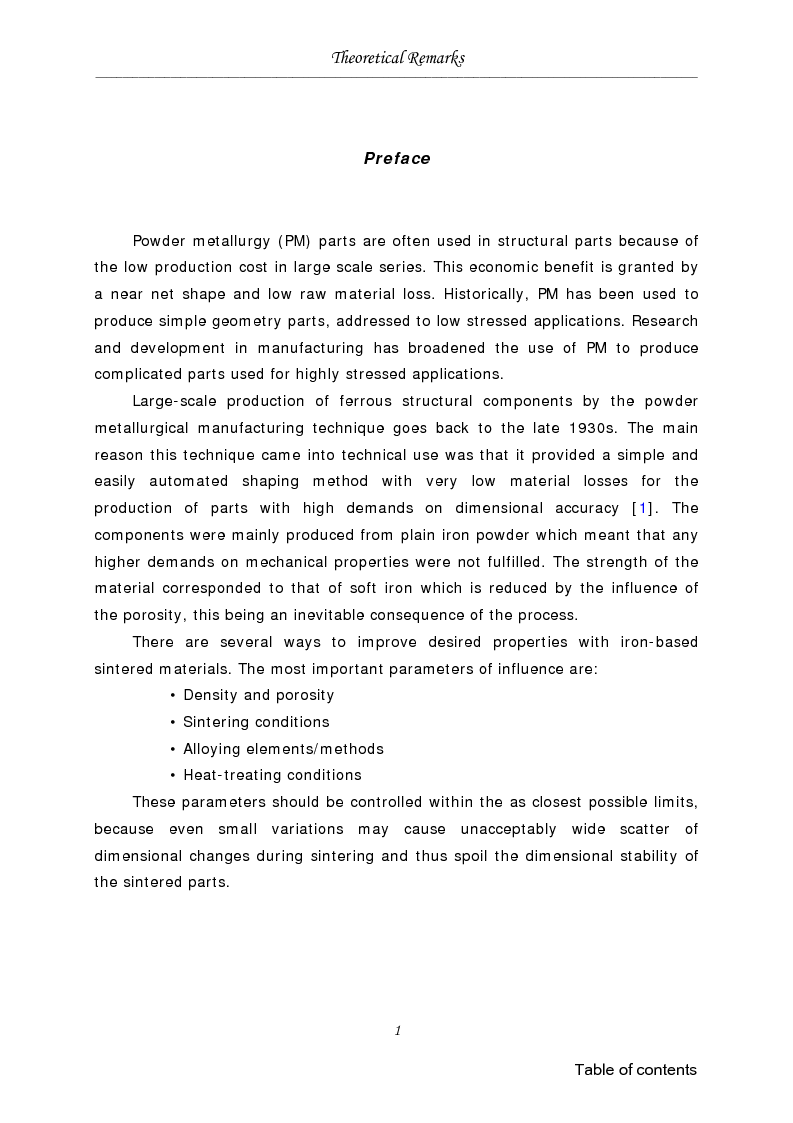
CONSULTA INTEGRALMENTE QUESTA TESI
La consultazione è esclusivamente in formato digitale .PDF
Acquista
Informazioni tesi
Autore: | Vanya Stoyanova |
Tipo: | Tesi di Dottorato |
Dottorato in | Dottorato di Ricerca in Ingegneria dei Materiali |
Anno: | 2005 |
Docente/Relatore: | Molinari Alberto |
Istituito da: | Università degli Studi di Trento |
Dipartimento: | DIMTI |
Lingua: | Inglese |
Num. pagine: | 204 |
Forse potrebbe interessarti la tesi:
Analisi frattografica di una massa battente
FAQ
Come consultare una tesi
Il pagamento può essere effettuato tramite carta di credito/carta prepagata, PayPal, bonifico bancario.
Confermato il pagamento si potrà consultare i file esclusivamente in formato .PDF accedendo alla propria Home Personale. Si potrà quindi procedere a salvare o stampare il file.
Maggiori informazioni
Perché consultare una tesi?
- perché affronta un singolo argomento in modo sintetico e specifico come altri testi non fanno;
- perché è un lavoro originale che si basa su una ricerca bibliografica accurata;
- perché, a differenza di altri materiali che puoi reperire online, una tesi di laurea è stata verificata da un docente universitario e dalla commissione in sede d'esame. La nostra redazione inoltre controlla prima della pubblicazione la completezza dei materiali e, dal 2009, anche l'originalità della tesi attraverso il software antiplagio Compilatio.net.
Clausole di consultazione
- L'utilizzo della consultazione integrale della tesi da parte dell'Utente che ne acquista il diritto è da considerarsi esclusivamente privato.
- Nel caso in cui l’utente che consulta la tesi volesse citarne alcune parti, dovrà inserire correttamente la fonte, come si cita un qualsiasi altro testo di riferimento bibliografico.
- L'Utente è l'unico ed esclusivo responsabile del materiale di cui acquista il diritto alla consultazione. Si impegna a non divulgare a mezzo stampa, editoria in genere, televisione, radio, Internet e/o qualsiasi altro mezzo divulgativo esistente o che venisse inventato, il contenuto della tesi che consulta o stralci della medesima. Verrà perseguito legalmente nel caso di riproduzione totale e/o parziale su qualsiasi mezzo e/o su qualsiasi supporto, nel caso di divulgazione nonché nel caso di ricavo economico derivante dallo sfruttamento del diritto acquisito.
Vuoi tradurre questa tesi?
Per raggiungerlo, è fondamentale superare la barriera rappresentata dalla lingua. Ecco perché cerchiamo persone disponibili ad effettuare la traduzione delle tesi pubblicate nel nostro sito.
Per tradurre questa tesi clicca qui »
Scopri come funziona »
DUBBI? Contattaci
Contatta la redazione a
[email protected]
Parole chiave
Tesi correlate
Non hai trovato quello che cercavi?
Abbiamo più di 45.000 Tesi di Laurea: cerca nel nostro database
Oppure consulta la sezione dedicata ad appunti universitari selezionati e pubblicati dalla nostra redazione
Ottimizza la tua ricerca:
- individua con precisione le parole chiave specifiche della tua ricerca
- elimina i termini non significativi (aggettivi, articoli, avverbi...)
- se non hai risultati amplia la ricerca con termini via via più generici (ad esempio da "anziano oncologico" a "paziente oncologico")
- utilizza la ricerca avanzata
- utilizza gli operatori booleani (and, or, "")
Idee per la tesi?
Scopri le migliori tesi scelte da noi sugli argomenti recenti
Come si scrive una tesi di laurea?
A quale cattedra chiedere la tesi? Quale sarà il docente più disponibile? Quale l'argomento più interessante per me? ...e quale quello più interessante per il mondo del lavoro?
Scarica gratuitamente la nostra guida "Come si scrive una tesi di laurea" e iscriviti alla newsletter per ricevere consigli e materiale utile.
La tesi l'ho già scritta,
ora cosa ne faccio?
La tua tesi ti ha aiutato ad ottenere quel sudato titolo di studio, ma può darti molto di più: ti differenzia dai tuoi colleghi universitari, mostra i tuoi interessi ed è un lavoro di ricerca unico, che può essere utile anche ad altri.
Il nostro consiglio è di non sprecare tutto questo lavoro:
È ora di pubblicare la tesi