Analisi del reparto macchine utensili e della gestione di una commessa in una realtà del settore industrial automation
L’elaborato, prova finale del corso di laurea in Ingegneria della Produzione Industriale Meccanica, ha come obbiettivo principale l’analisi di un processo produttivo in un contesto “job shop” (produzione su commessa). L’esperienza da cui deriva questo elaborato è maturata durante il tirocinio universitario presso una azienda marchigiana, la QS Group di Cerreto D’Esi (AN), che progetta e costruisce linee di produzione automatiche dedicate alle aziende produttrici di elettrodomestici.L’ambiente produttivo “job shop” implica la creazione di progetti unici e particolarmente complessi e la creazione di un sistema produttivo estremamente flessibile. Si necessita quindi di macchinari e attrezzature con capacità generiche, idonei a effettuare un ampio spettro di lavorazioni, il “layout” è in genere organizzato per reparti, secondo criteri di omogeneità delle lavorazioni realizzabili.
L’iter gestionale che generalmente segue un progetto di questo tipo è descritto nel capitolo 4, anche con l’ausilio di diagrammi di flusso, così come i software impiegati e il sistema di codici utilizzato nella identificazione di ogni componente delle linee.
I primi aspetti analizzati specifici delle lavorazioni meccaniche sono stati i tempi e i metodi di lavorazione (capitolo 6).
Durante il caricamento dei centri di lavoro, molta attenzione va posta nell’assegnazione dei particolari, seguendo un criterio di omogeneità delle seguenti caratteristiche: materiale, dimensioni, complessità, forma.
Questo accorgimento riduce i tempi in maniera drastica rispetto un tipo di assegnazione di lavorazioni basato solo sulle scadenze imposte, la lavorazione di pezzi dello stesso materiale e di simili dimensioni porta a non dover cambiare ogni volta componenti utensili o metodi di fissaggio, mentre la complessità del pezzo da lavorare deve essere adeguata al centro di lavoro scelto, senza quindi sotto impiegare o sovra impiegare macchine utensili più o meno prestazionali.
Un ulteriore metodo per poter ridurre i tempi di set up delle macchine CNC potrebbe derivare dal memorizzare su di un computer laptop i programmi di lavorazione ISO dei particolari ridondanti, associati al relativo disegno, in questo modo, quando si assegnano determinate lavorazioni si può confrontare il disegno tecnico con i disegni in archivio, richiamando poi il codice istantaneamente.
Sempre nel capitolo 6 si fa riferimento agli strumenti usati per il monitoraggio della produzione, intesa sempre in ambito di reparto macchine utensili, in questo caso era già presente un format, foglio di calcolo Excel dove si riportano tutte le lavorazioni effettuate di ogni singolo particolare, è utile nel tenere sotto controllo la tempistica e la rintracciabilità di ogni componente, le informazioni che contiene sono: codice completo del singolo particolare, lead time di lavorazione previsto, stato di completamento, operatore a cui è assegnato, data di assegnazione, data completamento.
Questo format è stato modificato personalmente aggiungendo le colonne “work in process” e “note”, per poter gestire meglio quei materiali non ancora completati, ma ad un certo stadio di lavorazione, o che necessitano di trattamenti post lavorazione (figure 25 e 26).
Per avere presente quanta autonomia hanno i centri di lavoro è stato sviluppato personalmente un grafico dinamico di Excel (figura 27 e 28): si usano i lead time dei lavori assegnati ancora da completare (sfruttando i filtri di Excel), divisi per operatore, e si vede il monte ore assegnato, si prevede così il centro di lavoro che si scaricherà per primo e ci si anticipa nel preparare il materiale adatto pronto da assegnare. Questa informazione facilita anche l’aggregazione di particolari simili nelle caratteristiche già indicate per ridurre il lead time.
Ulteriori sviluppi, nella problematica delle performances produttive si possono trovare nel capitolo 8, con riferimento anche al problema dello slittamento dei piani produttivi, e delle conseguenze economicamente penalizzanti. Si cerca inoltre di arrivare alla definizione di soluzioni migliorative.
Concludendo, si possono quindi definire le principali problematiche relative ai sistemi produttivi “job shop”:
• flessibilità della capacità produttiva interna
• contenimento delle inefficienze
• rispetto delle tempistiche
Far leva su questi elementi si può portare a dei risultati quali:
• riduzione dei “rush” (urgenze)
• minore impiego di ore lavorative straordinarie
• meno dipendenza dai fornitori
CONSULTA INTEGRALMENTE QUESTA TESI
La consultazione è esclusivamente in formato digitale .PDF
Acquista
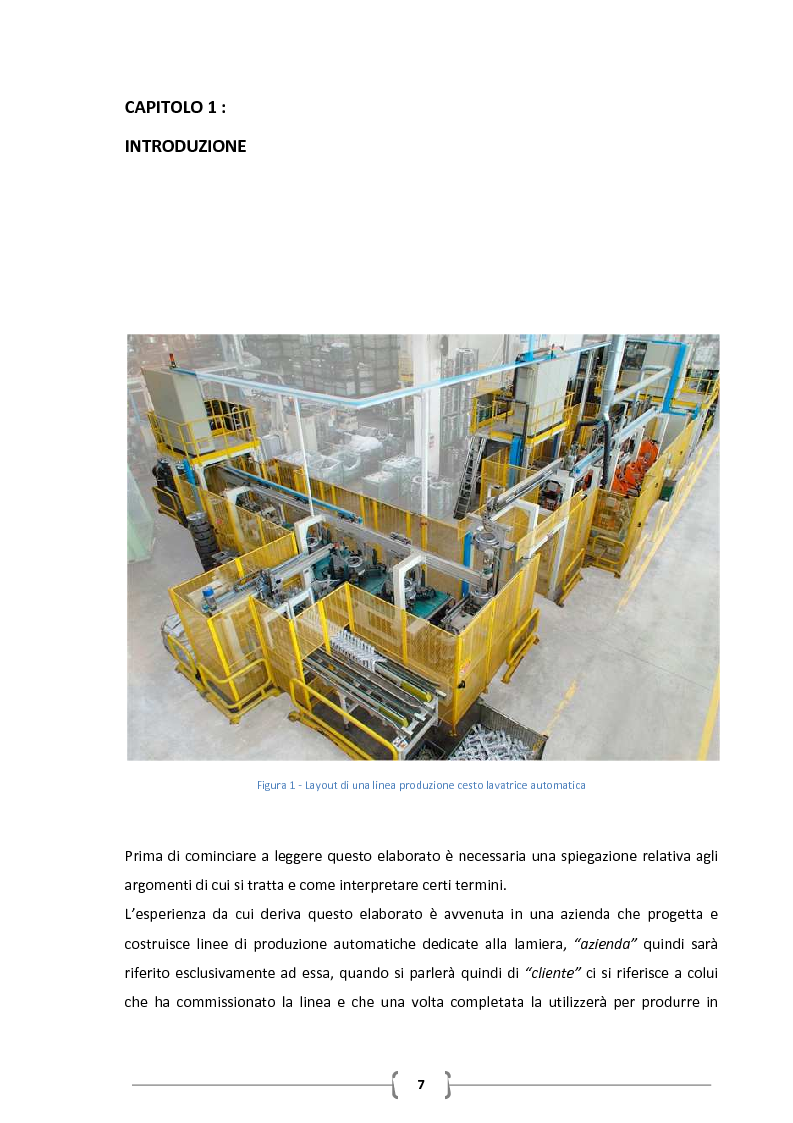
CONSULTA INTEGRALMENTE QUESTA TESI
La consultazione è esclusivamente in formato digitale .PDF
Acquista
Informazioni tesi
Autore: | Carlo Andrea Ceccoli |
Tipo: | Laurea I ciclo (triennale) |
Anno: | 2007-08 |
Università: | Università Politecnica delle Marche |
Facoltà: | Ingegneria |
Corso: | Ingegneria industriale |
Lingua: | Italiano |
Num. pagine: | 86 |
Forse potrebbe interessarti la tesi:
Riforme pro concorrenziali e crescita della produttività nell'Unione Europea
FAQ
Come consultare una tesi
Il pagamento può essere effettuato tramite carta di credito/carta prepagata, PayPal, bonifico bancario.
Confermato il pagamento si potrà consultare i file esclusivamente in formato .PDF accedendo alla propria Home Personale. Si potrà quindi procedere a salvare o stampare il file.
Maggiori informazioni
Perché consultare una tesi?
- perché affronta un singolo argomento in modo sintetico e specifico come altri testi non fanno;
- perché è un lavoro originale che si basa su una ricerca bibliografica accurata;
- perché, a differenza di altri materiali che puoi reperire online, una tesi di laurea è stata verificata da un docente universitario e dalla commissione in sede d'esame. La nostra redazione inoltre controlla prima della pubblicazione la completezza dei materiali e, dal 2009, anche l'originalità della tesi attraverso il software antiplagio Compilatio.net.
Clausole di consultazione
- L'utilizzo della consultazione integrale della tesi da parte dell'Utente che ne acquista il diritto è da considerarsi esclusivamente privato.
- Nel caso in cui l’utente che consulta la tesi volesse citarne alcune parti, dovrà inserire correttamente la fonte, come si cita un qualsiasi altro testo di riferimento bibliografico.
- L'Utente è l'unico ed esclusivo responsabile del materiale di cui acquista il diritto alla consultazione. Si impegna a non divulgare a mezzo stampa, editoria in genere, televisione, radio, Internet e/o qualsiasi altro mezzo divulgativo esistente o che venisse inventato, il contenuto della tesi che consulta o stralci della medesima. Verrà perseguito legalmente nel caso di riproduzione totale e/o parziale su qualsiasi mezzo e/o su qualsiasi supporto, nel caso di divulgazione nonché nel caso di ricavo economico derivante dallo sfruttamento del diritto acquisito.
Vuoi tradurre questa tesi?
Per raggiungerlo, è fondamentale superare la barriera rappresentata dalla lingua. Ecco perché cerchiamo persone disponibili ad effettuare la traduzione delle tesi pubblicate nel nostro sito.
Per tradurre questa tesi clicca qui »
Scopri come funziona »
DUBBI? Contattaci
Contatta la redazione a
[email protected]
Parole chiave
Tesi correlate
Non hai trovato quello che cercavi?
Abbiamo più di 45.000 Tesi di Laurea: cerca nel nostro database
Oppure consulta la sezione dedicata ad appunti universitari selezionati e pubblicati dalla nostra redazione
Ottimizza la tua ricerca:
- individua con precisione le parole chiave specifiche della tua ricerca
- elimina i termini non significativi (aggettivi, articoli, avverbi...)
- se non hai risultati amplia la ricerca con termini via via più generici (ad esempio da "anziano oncologico" a "paziente oncologico")
- utilizza la ricerca avanzata
- utilizza gli operatori booleani (and, or, "")
Idee per la tesi?
Scopri le migliori tesi scelte da noi sugli argomenti recenti
Come si scrive una tesi di laurea?
A quale cattedra chiedere la tesi? Quale sarà il docente più disponibile? Quale l'argomento più interessante per me? ...e quale quello più interessante per il mondo del lavoro?
Scarica gratuitamente la nostra guida "Come si scrive una tesi di laurea" e iscriviti alla newsletter per ricevere consigli e materiale utile.
La tesi l'ho già scritta,
ora cosa ne faccio?
La tua tesi ti ha aiutato ad ottenere quel sudato titolo di studio, ma può darti molto di più: ti differenzia dai tuoi colleghi universitari, mostra i tuoi interessi ed è un lavoro di ricerca unico, che può essere utile anche ad altri.
Il nostro consiglio è di non sprecare tutto questo lavoro:
È ora di pubblicare la tesi