Influence of Profile Modifications on Transmission Error and Noise of Spur Gears
Gear transmission error is defined as the difference between the actual position of the driven gear and its theoretical one in case of prefect transmission. The main causes of transmission error are the deformation of the meshing teeth under the applied load, as well as the manufacturing and assembling errors. In quasi-static conditions, transmission error is called static transmission error and it can be thought of as a little vibration, originating at the gear mesh, pushing the driven gear backwards and forwards. This little imposed displacement, responsible of impacts at the beginning of the gear mesh and vibrations of the gear blanks, is unanimously considered as a powerful indicator of gears vibrations and noise. The vibrations originating at the gear mesh can be amplified by the dynamics of the gear transmission and they can turn into a bigger vibration called dynamic transmission error; then, this vibration can propagate through shafts and supports, reaching the gearbox walls that radiate them outwards as loudspeakers, producing noise. The gear designer can reduce transmission error both statically, with opportune profile modifications, and dynamically, by means of an accurate study of the dynamics of the gear transmission. Nevertheless, the validation of any theoretical model, available since design phase, requires experimental tests.
In this study, the influence of profile modifications on noise and transmission error of spur gears is investigated. A test facility is setup in order to measure both transmission error and noise of parallel axis gear sets. The setup of the test rig includes the development of a gear casing for the lubrication of the gear sets and for an easy and quick mounting and dismounting of the gears to be tested; the same gear casing is designed according to the encoders tolerances prescribed in the data sheet, in order to guarantee the measurement accuracy specified by the manufacturer. At the same time, a measurement system is designed to measure both static and dynamic transmission error using optical encoders; the measurement system is based on an innovative data acquisition and elaboration procedure, representing an alternative to the common phase difference techniques employed in traditional transmission error measurements. By means of this procedure, sampled data are reconstructed by interpolation and, using the once-per-revolution signals of the two encoders, all TE measurements can be made from a common pair of teeth in contact.
Next, a model for the prediction of static transmission error is developed, considering the effect of the tooth bending compliance, the Hertzian compliance and the tooth base rotation on gear mesh stiffness. The model calculates static transmission error in function of both the applied torque and the gears geometry; its validation is performed both numerically, comparing its results to those ones obtained using an existing commercial software, and experimentally. To this aim, four gear sets, with the same macro-geometry, but different profile modifications, are considered and static transmission error is measured for different values of input torques on the test facility previously described; experimental results are compared to theoretical ones.
Then, different dynamic models of the test facility are considered, in order to investigate the level of complexity necessary to accurately describe the dynamics of the test rig. Starting from a two degrees of freedom lumped parameters linear model, excited at the gear mesh by an imposed displacement constraint modelling static transmission error, the scheme complexity is increased up to consider a finite elements model of the gear transmission. Couplings between transverse and torsional vibration, due to bearings and shafts compliances, are investigated, while the validation of the models is performed measuring dynamic transmission error up to 3000 rpm.
Finally, the influence of profile modifications on gear noise is investigated. The sound pressure of the four gear sets is measured for different values of speed and torque. The comparison between experimental and theoretical results proves the close correspondence between measured sound pressure levels and dynamic mesh forces predicted on the basis of static transmission error measurements. More accurate gear noise measurements are presented, showing that the most significant sound emission occurs in correspondence of the gear mesh and that the biggest harmonic amplification is found in correspondence of the vibration mode associated to the highest mesh stiffness excitation.
CONSULTA INTEGRALMENTE QUESTA TESI
La consultazione è esclusivamente in formato digitale .PDF
Acquista
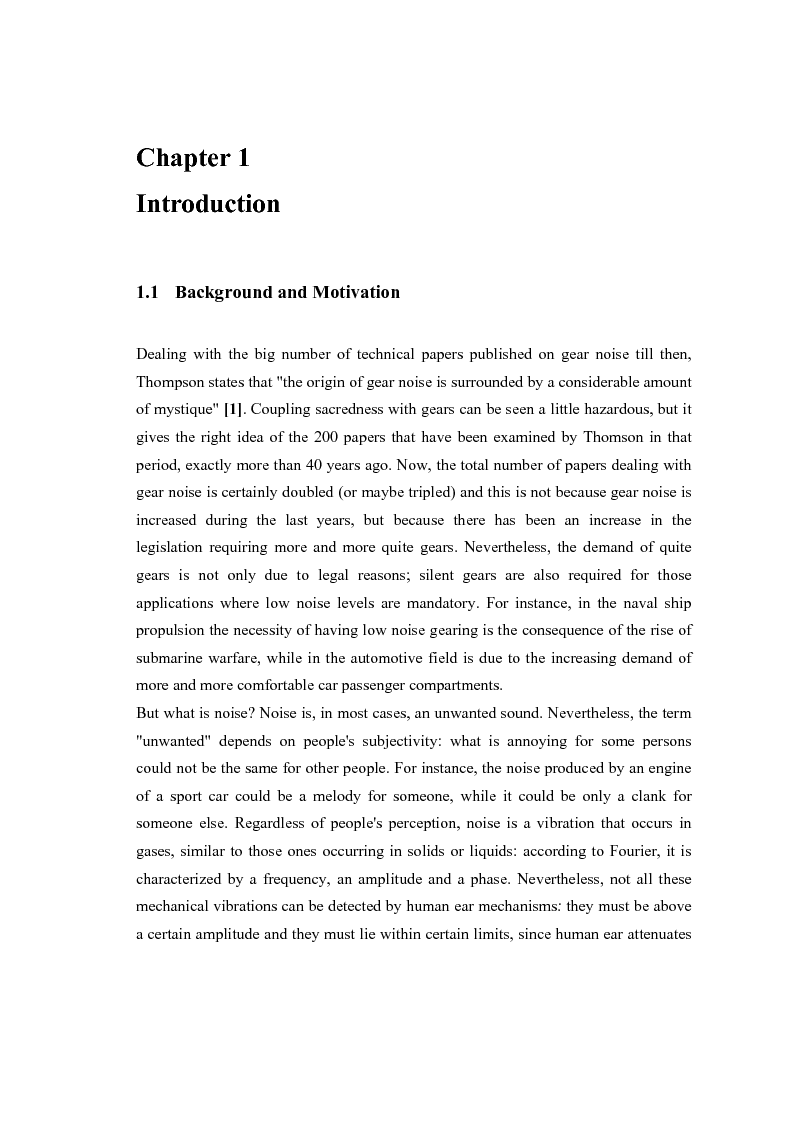
CONSULTA INTEGRALMENTE QUESTA TESI
La consultazione è esclusivamente in formato digitale .PDF
Acquista
Informazioni tesi
Autore: | Fabrizio Rossi |
Tipo: | Tesi di Dottorato |
Dottorato in | Ingegneria dei Sistemi Meccanici |
Anno: | 2010 |
Docente/Relatore: | Piermaria Davoli |
Correlatore: | CarloGorlaGiuseppeBoni |
Istituito da: | Politecnico di Milano |
Dipartimento: | Dipartimento di Meccanica |
Lingua: | Inglese |
Num. pagine: | 240 |
Forse potrebbe interessarti la tesi:
Allestimento di un banco prova per il test di micro motori ''Squiggle''
FAQ
Come consultare una tesi
Il pagamento può essere effettuato tramite carta di credito/carta prepagata, PayPal, bonifico bancario.
Confermato il pagamento si potrà consultare i file esclusivamente in formato .PDF accedendo alla propria Home Personale. Si potrà quindi procedere a salvare o stampare il file.
Maggiori informazioni
Perché consultare una tesi?
- perché affronta un singolo argomento in modo sintetico e specifico come altri testi non fanno;
- perché è un lavoro originale che si basa su una ricerca bibliografica accurata;
- perché, a differenza di altri materiali che puoi reperire online, una tesi di laurea è stata verificata da un docente universitario e dalla commissione in sede d'esame. La nostra redazione inoltre controlla prima della pubblicazione la completezza dei materiali e, dal 2009, anche l'originalità della tesi attraverso il software antiplagio Compilatio.net.
Clausole di consultazione
- L'utilizzo della consultazione integrale della tesi da parte dell'Utente che ne acquista il diritto è da considerarsi esclusivamente privato.
- Nel caso in cui l’utente che consulta la tesi volesse citarne alcune parti, dovrà inserire correttamente la fonte, come si cita un qualsiasi altro testo di riferimento bibliografico.
- L'Utente è l'unico ed esclusivo responsabile del materiale di cui acquista il diritto alla consultazione. Si impegna a non divulgare a mezzo stampa, editoria in genere, televisione, radio, Internet e/o qualsiasi altro mezzo divulgativo esistente o che venisse inventato, il contenuto della tesi che consulta o stralci della medesima. Verrà perseguito legalmente nel caso di riproduzione totale e/o parziale su qualsiasi mezzo e/o su qualsiasi supporto, nel caso di divulgazione nonché nel caso di ricavo economico derivante dallo sfruttamento del diritto acquisito.
Vuoi tradurre questa tesi?
Per raggiungerlo, è fondamentale superare la barriera rappresentata dalla lingua. Ecco perché cerchiamo persone disponibili ad effettuare la traduzione delle tesi pubblicate nel nostro sito.
Per tradurre questa tesi clicca qui »
Scopri come funziona »
DUBBI? Contattaci
Contatta la redazione a
[email protected]
Parole chiave
Tesi correlate
Non hai trovato quello che cercavi?
Abbiamo più di 45.000 Tesi di Laurea: cerca nel nostro database
Oppure consulta la sezione dedicata ad appunti universitari selezionati e pubblicati dalla nostra redazione
Ottimizza la tua ricerca:
- individua con precisione le parole chiave specifiche della tua ricerca
- elimina i termini non significativi (aggettivi, articoli, avverbi...)
- se non hai risultati amplia la ricerca con termini via via più generici (ad esempio da "anziano oncologico" a "paziente oncologico")
- utilizza la ricerca avanzata
- utilizza gli operatori booleani (and, or, "")
Idee per la tesi?
Scopri le migliori tesi scelte da noi sugli argomenti recenti
Come si scrive una tesi di laurea?
A quale cattedra chiedere la tesi? Quale sarà il docente più disponibile? Quale l'argomento più interessante per me? ...e quale quello più interessante per il mondo del lavoro?
Scarica gratuitamente la nostra guida "Come si scrive una tesi di laurea" e iscriviti alla newsletter per ricevere consigli e materiale utile.
La tesi l'ho già scritta,
ora cosa ne faccio?
La tua tesi ti ha aiutato ad ottenere quel sudato titolo di studio, ma può darti molto di più: ti differenzia dai tuoi colleghi universitari, mostra i tuoi interessi ed è un lavoro di ricerca unico, che può essere utile anche ad altri.
Il nostro consiglio è di non sprecare tutto questo lavoro:
È ora di pubblicare la tesi