Realizzazione di una struttura pilota per lo studio sperimentale delle tecniche di formatura con fluidi in pressione
Il costante intensificarsi della competizione mondiale, unito alle richieste del mercato rivolte ad una maggiore attenzione per la sicurezza e per il risparmio energetico, ed alle esigenze in materia di salvaguardia e difesa dell’ambiente ha spinto l’industria a rivolgersi verso nuove tecnologie e nuovi materiali per cercare di soddisfare tali bisogni.
Particolarmente significativi sono stati gli sviluppi nell’industria dei veicoli, la quale da sempre ha avuto la necessità di dover trovare un giusto compromesso fra basso peso dei materiali ed un’adeguata resistenza degli stessi. Sono possibili due strade per la riduzione dei pesi: l’introduzione di nuovi materiali e il miglior uso dei materiali tradizionali. Nel primo caso, il fattore limitante è rappresentato soprattutto dal costo (per una riduzione di peso del 10-20% si stima un incremento di costo del 5-6%). Nel secondo caso, l’affinamento della progettazione e l’uso di nuovi processi di produzione consentono di ridurre il peso a parità di rigidezza, utilizzando al meglio le caratteristiche dei materiali tradizionali.
Tra i nuovi processi produttivi c’è la formatura con fluidi in pressione (generalmente chiamata idroformatura), che grazie all’impulso ricevuto dall’industria automobilistica, ha avuto un incremento di applicazioni industriali in diversi settori.
Soprattutto l’idroformatura tubolare con la sua capacità di realizzare geometrie complesse mediante fluidi in pressione, si è dimostrata in grado di offrire interessanti potenzialità sia dal punto di vista tecnico che da quello economico. In generale il processo di idroformatura è una tecnica di deformazione a freddo e si basa sull’espansione di un semiprodotto tubolare che, mediante un fluido (olio o acqua) in pressione, viene spinto a ricopiare la geometria di uno stampo.
I più importanti aspetti tecnici ed economici dell’idroformatura sono: la costruzione del componente in un pezzo singolo, che elimina le operazioni di saldatura; il processo di calibrazione, che assicura un elevato grado di accuratezza dei contorni e, in generale, delle dimensioni del componente idroformato anche sui lotti di grandi numeri; un elevato incrudimento del materiale, che comporta un più elevato grado di rigidità torsionale nel componente idroformato; le caratteristiche di recupero elastico dei componenti idroformati, che, grazie all’uniformità delle deformazioni e quindi delle tensioni, in genere sono meno pronunciate rispetto al caso di parti ottenute tramite saldatura; l’abbattimento dei costi per produzioni in serie, derivato dall’eliminazione di passi intermedi di stampaggio e di tutte le operazioni di assemblaggio delle parti dei componenti. Per questo, spesso è possibile addirittura ridurre lo spessore della parete del componente rispetto a quanto si deve avere con componenti ottenuti per fusione o stampaggio.
L’obiettivo di questo lavoro di tesi è quello di realizzare un’attrezzatura per lo stampaggio di lamiere sottili, idonea a più processi di formatura, da quello d’imbutitura convenzionale a quelli speciali di Hydromechanical Deep Drawing (HDD o idroformatura meccanica) e di idroformatura (Hydroforming); tra i requisiti di tale attrezzatura anche quello di richiedere un impegno economico e una complessità realizzativa accettabile.
Per verificare la fattibilità dei processi, le possibilità e le potenzialità dell’attrezzature progettate e realizzate, sono stati indagati alcuni parametri geometrici e di processo, in modo da testare le attrezzature in diverse condizioni di funzionamento; anche la scelta di sperimentare due materiali diversi e di diverso spessore, quali l’acciaio inox AISI 304 e l’acciaio commerciale FeP04, va vista in quest’ottica generale del progetto.
Il presente lavoro si compone essenzialmente di quattro capitoli, dove nel primo viene descritto il processo di profondo stampaggio con le relative problematiche, nel secondo si descrivono le tecniche speciali di formatura e in particolar modo l’idroformatura di tubi e lamiere. Nel terzo capitolo è affrontata la fase progettuale delle attrezzature e viene descritta la metodologia adottata per l’esecuzione delle prove sperimentali; mentre il quarto capitolo riassume i risultati dell’indagine sperimentale condotta sui due tipi di materiali con i diversi processi d’imbutitura.
CONSULTA INTEGRALMENTE QUESTA TESI
La consultazione è esclusivamente in formato digitale .PDF
Acquista
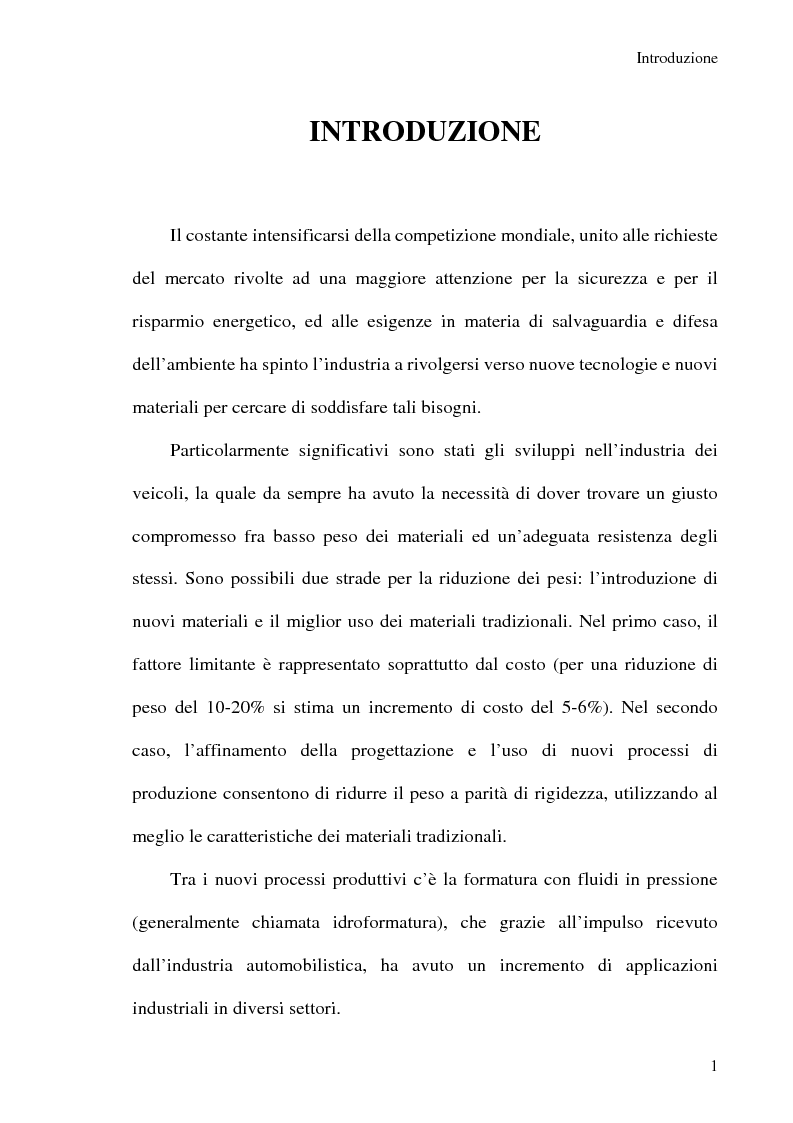
CONSULTA INTEGRALMENTE QUESTA TESI
La consultazione è esclusivamente in formato digitale .PDF
Acquista
Informazioni tesi
Autore: | Donato Grimaldi |
Tipo: | Tesi di Laurea |
Anno: | 1999-00 |
Università: | Politecnico di Bari |
Facoltà: | Ingegneria |
Corso: | Ingegneria Meccanica |
Lingua: | Italiano |
Num. pagine: | 203 |
Forse potrebbe interessarti la tesi:
Studio tecnologico-economico sull’applicabilità dell’idroformatura a componenti metallici per articoli casalinghi: il caso Alessi
FAQ
Come consultare una tesi
Il pagamento può essere effettuato tramite carta di credito/carta prepagata, PayPal, bonifico bancario.
Confermato il pagamento si potrà consultare i file esclusivamente in formato .PDF accedendo alla propria Home Personale. Si potrà quindi procedere a salvare o stampare il file.
Maggiori informazioni
Perché consultare una tesi?
- perché affronta un singolo argomento in modo sintetico e specifico come altri testi non fanno;
- perché è un lavoro originale che si basa su una ricerca bibliografica accurata;
- perché, a differenza di altri materiali che puoi reperire online, una tesi di laurea è stata verificata da un docente universitario e dalla commissione in sede d'esame. La nostra redazione inoltre controlla prima della pubblicazione la completezza dei materiali e, dal 2009, anche l'originalità della tesi attraverso il software antiplagio Compilatio.net.
Clausole di consultazione
- L'utilizzo della consultazione integrale della tesi da parte dell'Utente che ne acquista il diritto è da considerarsi esclusivamente privato.
- Nel caso in cui l’utente che consulta la tesi volesse citarne alcune parti, dovrà inserire correttamente la fonte, come si cita un qualsiasi altro testo di riferimento bibliografico.
- L'Utente è l'unico ed esclusivo responsabile del materiale di cui acquista il diritto alla consultazione. Si impegna a non divulgare a mezzo stampa, editoria in genere, televisione, radio, Internet e/o qualsiasi altro mezzo divulgativo esistente o che venisse inventato, il contenuto della tesi che consulta o stralci della medesima. Verrà perseguito legalmente nel caso di riproduzione totale e/o parziale su qualsiasi mezzo e/o su qualsiasi supporto, nel caso di divulgazione nonché nel caso di ricavo economico derivante dallo sfruttamento del diritto acquisito.
Vuoi tradurre questa tesi?
Per raggiungerlo, è fondamentale superare la barriera rappresentata dalla lingua. Ecco perché cerchiamo persone disponibili ad effettuare la traduzione delle tesi pubblicate nel nostro sito.
Scopri come funziona »
DUBBI? Contattaci
Contatta la redazione a
[email protected]
Parole chiave
Tesi correlate
Non hai trovato quello che cercavi?
Abbiamo più di 45.000 Tesi di Laurea: cerca nel nostro database
Oppure consulta la sezione dedicata ad appunti universitari selezionati e pubblicati dalla nostra redazione
Ottimizza la tua ricerca:
- individua con precisione le parole chiave specifiche della tua ricerca
- elimina i termini non significativi (aggettivi, articoli, avverbi...)
- se non hai risultati amplia la ricerca con termini via via più generici (ad esempio da "anziano oncologico" a "paziente oncologico")
- utilizza la ricerca avanzata
- utilizza gli operatori booleani (and, or, "")
Idee per la tesi?
Scopri le migliori tesi scelte da noi sugli argomenti recenti
Come si scrive una tesi di laurea?
A quale cattedra chiedere la tesi? Quale sarà il docente più disponibile? Quale l'argomento più interessante per me? ...e quale quello più interessante per il mondo del lavoro?
Scarica gratuitamente la nostra guida "Come si scrive una tesi di laurea" e iscriviti alla newsletter per ricevere consigli e materiale utile.
La tesi l'ho già scritta,
ora cosa ne faccio?
La tua tesi ti ha aiutato ad ottenere quel sudato titolo di studio, ma può darti molto di più: ti differenzia dai tuoi colleghi universitari, mostra i tuoi interessi ed è un lavoro di ricerca unico, che può essere utile anche ad altri.
Il nostro consiglio è di non sprecare tutto questo lavoro:
È ora di pubblicare la tesi