Lean Manufacturing nel settore manifatturiero: il caso Pramac
Questo lavoro riguarda l’applicazione dei principi della Lean Production all’interno della multinazionale Pramac S.p.A. di Casole val d’Elsa. Partendo da un focus limitato alla linea di produzione dei gruppi elettrogeni a catalogo, i concetti Lean si sono poi estesi all’intera azienda e anche all’esterno nei confronti dei principali fornitori. Lean Production è una filosofia di organizzazione del lavoro necessaria per tutte quelle imprese che vogliono essere competitive ed avere veloci tempi di risposta al cliente: queste caratteristiche sono indispensabili per tutte le organizzazioni che non vogliono soccombere all’invasione dei paesi low-cost come la Cina. Si basa sul concetto di caccia agli sprechi, ovvero eliminazione di attività che non aggiungono valore al cliente finale: solo così un’azienda può concentrare tutte le proprie risorse per realizzare un flusso produttivo guidato dalle richieste del mercato.
Pramac ha deciso di reagire alla crisi mondiale pianificando un intervento di Lean Manufacturing sul segmento di prodotto dei gruppi elettrogeni industriali (segmento che copre circa il 35% del mercato dei prodotto finiti Pramac). L’intervento è stato seguito nella fase di start-up dalla società di consulenza Bonfiglioli Consulting, la quale ha istruito il personale con i concetti base Lean e le linee guida di interveto. Gli obiettivi dichiarati dalla direzione consistono nell’aumento della produttività della catena di montaggio dei gruppi elettrogeni a catalogo, nella riduzione delle scorte (materie prime, semi-lavorati, work-in-process e prodotti finiti) e nella riduzione dei tempi di consegna dei prodotti al cliente finale.
Il progetto Lean Manufacturing è stato avviato a Febbraio 2011 sotto la guida del Plant Operations Manager Daniele Sargenti che si è posto come obiettivo della prima fase il recupero di produttività del 20% sui tempi standard della linea di assemblaggio. Nell’analisi preliminare vengono evidenziate due macro-famiglie di prodotto con ciclo di lavorazione costituito da sei macro-fasi svolte su una linea estremamente sbilanciata in termini di contenuto di lavoro per singola postazione. Inoltre risulta un’incidenza molto alta degli sprechi (circa il 50% del tempo di produzione).
I primi interventi sono stati pianificati sulla linea stessa, dove il carico di lavoro delle singole macchine è stato re-distribuito nelle dieci postazioni in accordo con l’euristica Ranked Positional Weight Technique (euristica per la risoluzione del problema PLI sul dimensionamento della linea). Successivamente è stato programmato un piano di intervento per l’eliminazione di tutte le attività senza valore aggiunto per il prodotto. Infine è stato re-disegnato il Lay-out organizzativo della linea (area Supermarket, carrelli Kit, aree di pre-montaggio) e definito un organigramma dei ruoli svolti dagli operatori.
La produzione a flusso tirato è iniziata a fine Giugno 2011. Attraverso indicatori relativi a produttività e qualità, sono stati analizzati i primi risultati ottenuti confrontando i dati di Marzo 2011 con quelli di Ottobre 2011 evidenziando: riduzione del tempo medio di processo del 30%; aumento dell’efficienza della linea del 17%; aumento medio dell’efficienza delle postazione del 28%; riduzione del Lead Time di attraversamento dalla materia prima al prodotti finito; riduzione delle attività generanti sprechi; riduzione delle non conformità mensili.
Il passo successivo è quello della conversione delle catene di fornitura ai principi snelli (Lean Supply Chain): senza questo passaggio non è possibile ottenere un flusso completamente guidato dalle richieste dei clienti. Al momento sono stati coinvolti tre fornitori tramite una gestione del materiale a Kanban, tipico strumento Lean di facile utilizzo. Questo ha permesso di rendere più soddisfacenti i valori del magazzino e delle giacenze sincronizzando le catene di fornitura con i processi interni.
Sull’onda di questi risultati l’azienda ha confermato il suo impegno nell’adottare il modello Lean Thinking come riferimento per tutti i processi di gestione interna ed esterna.
CONSULTA INTEGRALMENTE QUESTA TESI
La consultazione è esclusivamente in formato digitale .PDF
Acquista
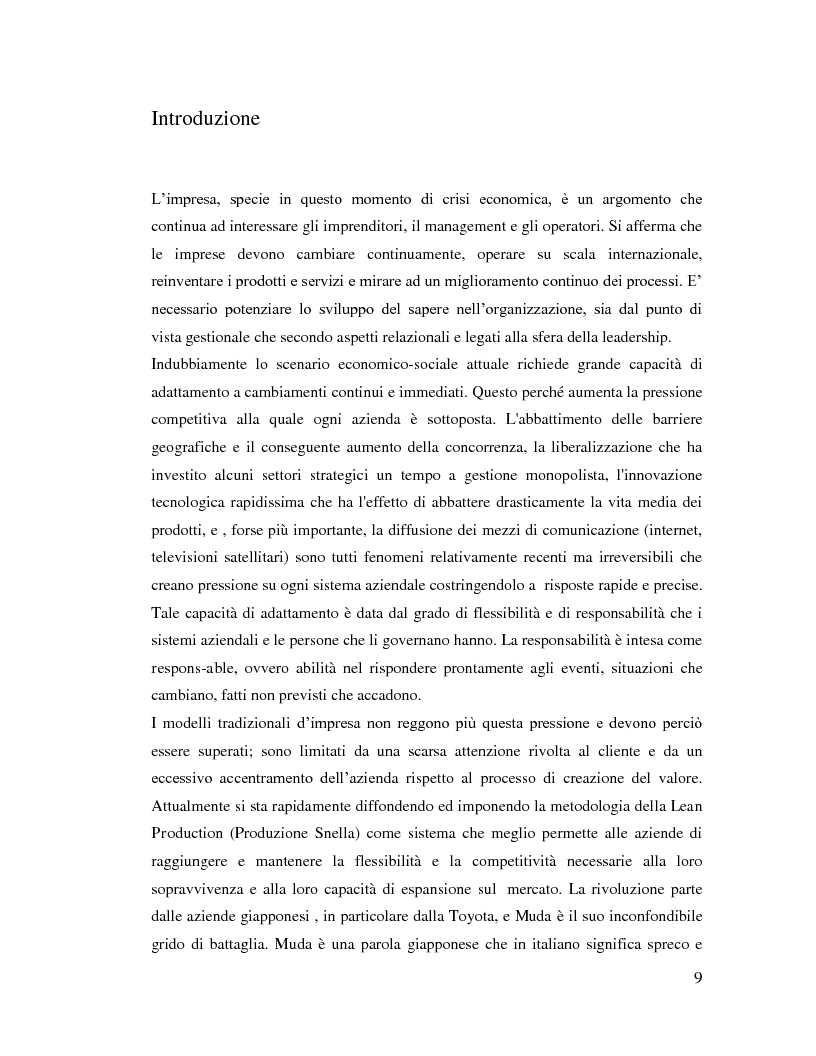
CONSULTA INTEGRALMENTE QUESTA TESI
La consultazione è esclusivamente in formato digitale .PDF
Acquista
Informazioni tesi
Autore: | Jacopo Guercini |
Tipo: | Tesi di Laurea Magistrale |
Anno: | 2010-11 |
Università: | Università degli Studi di Siena |
Facoltà: | Ingegneria |
Corso: | Ingegneria gestionale |
Lingua: | Italiano |
Num. pagine: | 125 |
Forse potrebbe interessarti la tesi:
Da Mirafiori a Melfi: La Fiat dal Fordismo alla Produzione Snella
FAQ
Come consultare una tesi
Il pagamento può essere effettuato tramite carta di credito/carta prepagata, PayPal, bonifico bancario.
Confermato il pagamento si potrà consultare i file esclusivamente in formato .PDF accedendo alla propria Home Personale. Si potrà quindi procedere a salvare o stampare il file.
Maggiori informazioni
Perché consultare una tesi?
- perché affronta un singolo argomento in modo sintetico e specifico come altri testi non fanno;
- perché è un lavoro originale che si basa su una ricerca bibliografica accurata;
- perché, a differenza di altri materiali che puoi reperire online, una tesi di laurea è stata verificata da un docente universitario e dalla commissione in sede d'esame. La nostra redazione inoltre controlla prima della pubblicazione la completezza dei materiali e, dal 2009, anche l'originalità della tesi attraverso il software antiplagio Compilatio.net.
Clausole di consultazione
- L'utilizzo della consultazione integrale della tesi da parte dell'Utente che ne acquista il diritto è da considerarsi esclusivamente privato.
- Nel caso in cui l’utente che consulta la tesi volesse citarne alcune parti, dovrà inserire correttamente la fonte, come si cita un qualsiasi altro testo di riferimento bibliografico.
- L'Utente è l'unico ed esclusivo responsabile del materiale di cui acquista il diritto alla consultazione. Si impegna a non divulgare a mezzo stampa, editoria in genere, televisione, radio, Internet e/o qualsiasi altro mezzo divulgativo esistente o che venisse inventato, il contenuto della tesi che consulta o stralci della medesima. Verrà perseguito legalmente nel caso di riproduzione totale e/o parziale su qualsiasi mezzo e/o su qualsiasi supporto, nel caso di divulgazione nonché nel caso di ricavo economico derivante dallo sfruttamento del diritto acquisito.
Vuoi tradurre questa tesi?
Per raggiungerlo, è fondamentale superare la barriera rappresentata dalla lingua. Ecco perché cerchiamo persone disponibili ad effettuare la traduzione delle tesi pubblicate nel nostro sito.
Per tradurre questa tesi clicca qui »
Scopri come funziona »
DUBBI? Contattaci
Contatta la redazione a
[email protected]
Parole chiave
Tesi correlate
Non hai trovato quello che cercavi?
Abbiamo più di 45.000 Tesi di Laurea: cerca nel nostro database
Oppure consulta la sezione dedicata ad appunti universitari selezionati e pubblicati dalla nostra redazione
Ottimizza la tua ricerca:
- individua con precisione le parole chiave specifiche della tua ricerca
- elimina i termini non significativi (aggettivi, articoli, avverbi...)
- se non hai risultati amplia la ricerca con termini via via più generici (ad esempio da "anziano oncologico" a "paziente oncologico")
- utilizza la ricerca avanzata
- utilizza gli operatori booleani (and, or, "")
Idee per la tesi?
Scopri le migliori tesi scelte da noi sugli argomenti recenti
Come si scrive una tesi di laurea?
A quale cattedra chiedere la tesi? Quale sarà il docente più disponibile? Quale l'argomento più interessante per me? ...e quale quello più interessante per il mondo del lavoro?
Scarica gratuitamente la nostra guida "Come si scrive una tesi di laurea" e iscriviti alla newsletter per ricevere consigli e materiale utile.
La tesi l'ho già scritta,
ora cosa ne faccio?
La tua tesi ti ha aiutato ad ottenere quel sudato titolo di studio, ma può darti molto di più: ti differenzia dai tuoi colleghi universitari, mostra i tuoi interessi ed è un lavoro di ricerca unico, che può essere utile anche ad altri.
Il nostro consiglio è di non sprecare tutto questo lavoro:
È ora di pubblicare la tesi