Processi idrometallurgici in scala di laboratorio per l'estrazione di oro da minerali (cnr roma)
L’oro è contenuto in tre distinte categorie di minerali:
1. minerali free-milling: l’oro può essere quasi completamente estratto mediante un adeguato trattamento di macinazione. Il successivo recupero del metallo prezioso è realizzato attraverso processi fisici quali flottazione, concentrazione per gravità o attraverso metodi chimici quali ad esempio la lisciviazione precedentemente descritta. Il recupero dell’oro da tali minerali è di solito alto (97%) ed i costi di operazione sono spesso relativamente bassi ed i costi di operazione di solito sono sempre relativamente bassi;
2. complessi base-metal: oltre all’oro contengono notevoli quantità di Cu, Zn, Pb, Ni. Il metallo prezioso viene separato dal minerale insieme ai solfuri dei metalli base mediante processi fisici e successivamente è recuperato dai solfuri attraverso processi di raffinazione;
3. minerali refrattari: l’oro non può essere estratto dal minerale in maniera soddisfacente neppure con una macinazione molto spinta. Nei minerali refrattari di riferimento, il metallo prezioso è incapsulato in inclusioni sulfuree (pirite, arsenopirite, stibnite, pirrotite, calcopirite) che riducono o impediscono l’accesso dell’agente lisciviante sul sito di reazione. Esistono anche altri tipi di minerali auriferi refrattari a base di carbonio. Con un trattamento diretto di lisciviazione sui minerali solfuri si ottengono rese di estrazione di oro non superiori in genere al 30%. Il graduale esaurimento dei giacimenti auriferi del primo tipo ed un significativo aumento del prezzo dell’oro ha diretto l’interesse dell’industria verso i minerali refrattari, contenenti il cosiddetto oro invisibile.
I minerali free-milling con dimensioni per l’80% minori di 75 micron, danno un recupero di oro molto alto, con una convenzionale cianurazione della durata di 20-30 ore. Viene aggiunto sufficiente cianuro per mantenere una concentrazione stabile intorno ai 100-250 ppm con un pH all’incirca pari a 10 fino alla fine della lisciviazione. Abbiamo visto che i minerali che non permettono di recuperare oro con una convenzionale cianurazione vengono chiamati refrattari. In questo capitolo i minerali che danno un recupero economicamente accettabile di oro col solo trattamento di cianurazione vengono definiti complessi, mentre abbiamo già detto che vengono chiamati refrattari quei minerali che danno un recupero di oro incompleto attraverso il solo uso del processo di cianurazione.
CONSULTA INTEGRALMENTE QUESTA TESI
La consultazione è esclusivamente in formato digitale .PDF
Acquista
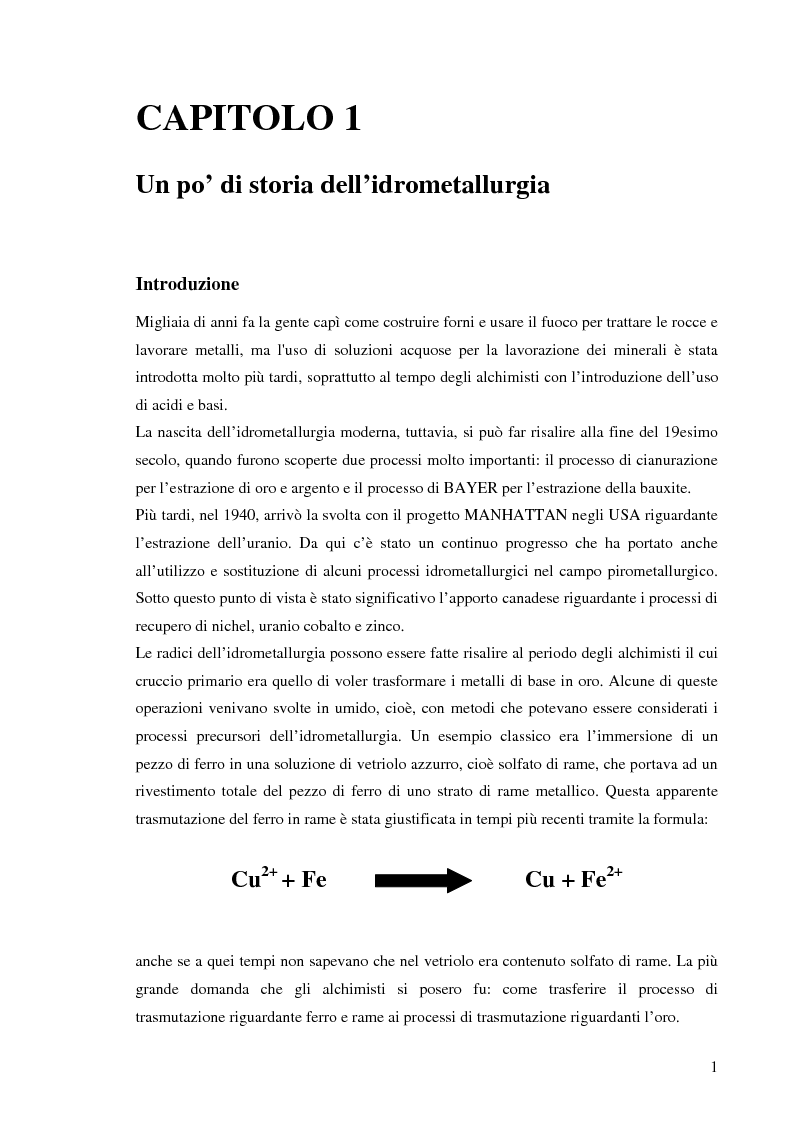
CONSULTA INTEGRALMENTE QUESTA TESI
La consultazione è esclusivamente in formato digitale .PDF
Acquista
L'unico servizio antiplagio competitivo nel prezzo che garantisce l'aiuto della nostra redazione nel controllo dei risultati.
Analisi sicura e anonima al 100%!
Ottieni un Certificato Antiplagio dopo la valutazione.
Informazioni tesi
Autore: | Lorenzo Marcelli |
Tipo: | Tesi di Laurea Magistrale |
Anno: | 2010-11 |
Università: | Università degli Studi dell'Aquila |
Facoltà: | Ingegneria |
Corso: | Ingegneria per l'Ambiente e il Territorio |
Relatore: | Francesco Vegliò |
Lingua: | Italiano |
Num. pagine: | 159 |
Forse potrebbe interessarti la tesi:
Infedeltà coniugale ed addebito della separazione
FAQ
Come consultare una tesi
Il pagamento può essere effettuato tramite carta di credito/carta prepagata, PayPal, bonifico bancario.
Confermato il pagamento si potrà consultare i file esclusivamente in formato .PDF accedendo alla propria Home Personale. Si potrà quindi procedere a salvare o stampare il file.
Maggiori informazioni
Perché consultare una tesi?
- perché affronta un singolo argomento in modo sintetico e specifico come altri testi non fanno;
- perché è un lavoro originale che si basa su una ricerca bibliografica accurata;
- perché, a differenza di altri materiali che puoi reperire online, una tesi di laurea è stata verificata da un docente universitario e dalla commissione in sede d'esame. La nostra redazione inoltre controlla prima della pubblicazione la completezza dei materiali e, dal 2009, anche l'originalità della tesi attraverso il software antiplagio Compilatio.net.
Clausole di consultazione
- L'utilizzo della consultazione integrale della tesi da parte dell'Utente che ne acquista il diritto è da considerarsi esclusivamente privato.
- Nel caso in cui l’utente che consulta la tesi volesse citarne alcune parti, dovrà inserire correttamente la fonte, come si cita un qualsiasi altro testo di riferimento bibliografico.
- L'Utente è l'unico ed esclusivo responsabile del materiale di cui acquista il diritto alla consultazione. Si impegna a non divulgare a mezzo stampa, editoria in genere, televisione, radio, Internet e/o qualsiasi altro mezzo divulgativo esistente o che venisse inventato, il contenuto della tesi che consulta o stralci della medesima. Verrà perseguito legalmente nel caso di riproduzione totale e/o parziale su qualsiasi mezzo e/o su qualsiasi supporto, nel caso di divulgazione nonché nel caso di ricavo economico derivante dallo sfruttamento del diritto acquisito.
Vuoi tradurre questa tesi?
Per raggiungerlo, è fondamentale superare la barriera rappresentata dalla lingua. Ecco perché cerchiamo persone disponibili ad effettuare la traduzione delle tesi pubblicate nel nostro sito.
Per tradurre questa tesi clicca qui »
Scopri come funziona »
DUBBI? Contattaci
Contatta la redazione a
[email protected]
Parole chiave
Tesi correlate
Non hai trovato quello che cercavi?
Abbiamo più di 45.000 Tesi di Laurea: cerca nel nostro database
Oppure consulta la sezione dedicata ad appunti universitari selezionati e pubblicati dalla nostra redazione
Ottimizza la tua ricerca:
- individua con precisione le parole chiave specifiche della tua ricerca
- elimina i termini non significativi (aggettivi, articoli, avverbi...)
- se non hai risultati amplia la ricerca con termini via via più generici (ad esempio da "anziano oncologico" a "paziente oncologico")
- utilizza la ricerca avanzata
- utilizza gli operatori booleani (and, or, "")
Idee per la tesi?
Scopri le migliori tesi scelte da noi sugli argomenti recenti
Come si scrive una tesi di laurea?
A quale cattedra chiedere la tesi? Quale sarà il docente più disponibile? Quale l'argomento più interessante per me? ...e quale quello più interessante per il mondo del lavoro?
Scarica gratuitamente la nostra guida "Come si scrive una tesi di laurea" e iscriviti alla newsletter per ricevere consigli e materiale utile.
La tesi l'ho già scritta,
ora cosa ne faccio?
La tua tesi ti ha aiutato ad ottenere quel sudato titolo di studio, ma può darti molto di più: ti differenzia dai tuoi colleghi universitari, mostra i tuoi interessi ed è un lavoro di ricerca unico, che può essere utile anche ad altri.
Il nostro consiglio è di non sprecare tutto questo lavoro:
È ora di pubblicare la tesi